Versiv LFL: Making Electromagnetic Solenoids Work Better
Versiv Low Friction Liners (LFL) are composites of fluoropolymer, with or without a reinforcing fibreglassfabric core.
These materials are increasingly being used in electromagnetic solenoids for automatic transmissions. They reduce the friction in moving applications in order to increase performance in terms of actuation speeds and power requirements.
Low coefficient of friction means more consistent movement forwards and backward, with minimum hysteresis or "slip-stick" effects. In specific applications, it minimizes the noise level generated by movement and performs consistently even at temperatures up to 200°C or higher throughout the device's lifetime.
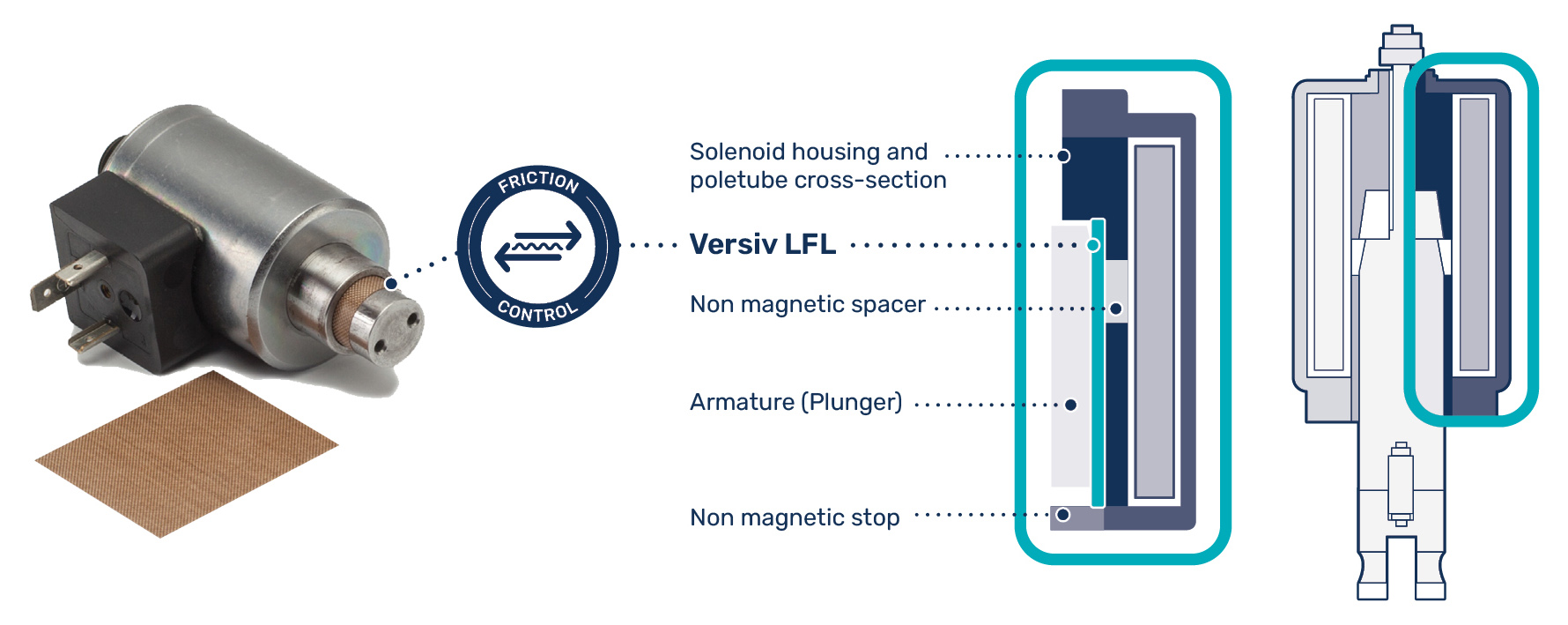
Low friction linings can replace messy greases, oils or lubricants that wear out or need frequent "topping-up". They can also replace metallic coatings, such as nickel or chrome, that are expensive and difficult to get in consistent quality.
The optimisation of hysteresis and low friction properties of LFL in electromagnetic solenoids have enabled improved transmission responsiveness and driver comfort. They also improve overall vehicle economics, with lower power consumption and reduced space and weight requirements.
We will work with you to help produce vehicles and systems that meet higher levels of fuel efficiency, increased life cycle, lower cost, and heightened performance.
Low hysteresis
Hysteresis testing of different Versiv Low Friction Linings (LFL) confirm that the force requirement is low and very stable and remains in the same range throughout the design lifetime of the solenoid. In addition, there is the benefit of no “stick-slip” effect.
Reduced power requirements
Due to the smaller air gap and low friction properties of Versiv LFL versus a stainless-steel tube, the energy consumed by the solenoid can be reduced by over 60%.
Consistent wear and low friction:
Versiv LFL have very consistent wear and low friction properties over their lifetime with little change in performance even after wear testing up to 10 million cycles. The lubricious and durable surface against the moving armature eliminates the risk of frictional “pick-up” or metallic contamination. They have been tested with contaminated “dirty” hydraulic and transmission oils and still performed satisfactorily.
Increased force
The available force and load capability can be increased by up to 65% with a Versiv LFL, thus enabling greater design flexibility.
Decreased thermal expansion
Stable at temperatures from -180°C to +260°C. Analysis of coefficients of thermal expansion of Versiv LFL indicates values of 50% to 60% less than cold rolled steel or stainless steel respectively for a similar temperature range.
Design flexibility
Versiv LFL offers improved design flexibility with more options for highly effective and economical designs due to an overall reduction in space and weight.
Our analysis indicates the following potential savings, in particular in the automotive applications: 67% reduction in Coil Mass, 28% reduction in Solenoid Mass, and 32% reduction in Solenoid Package Volume.