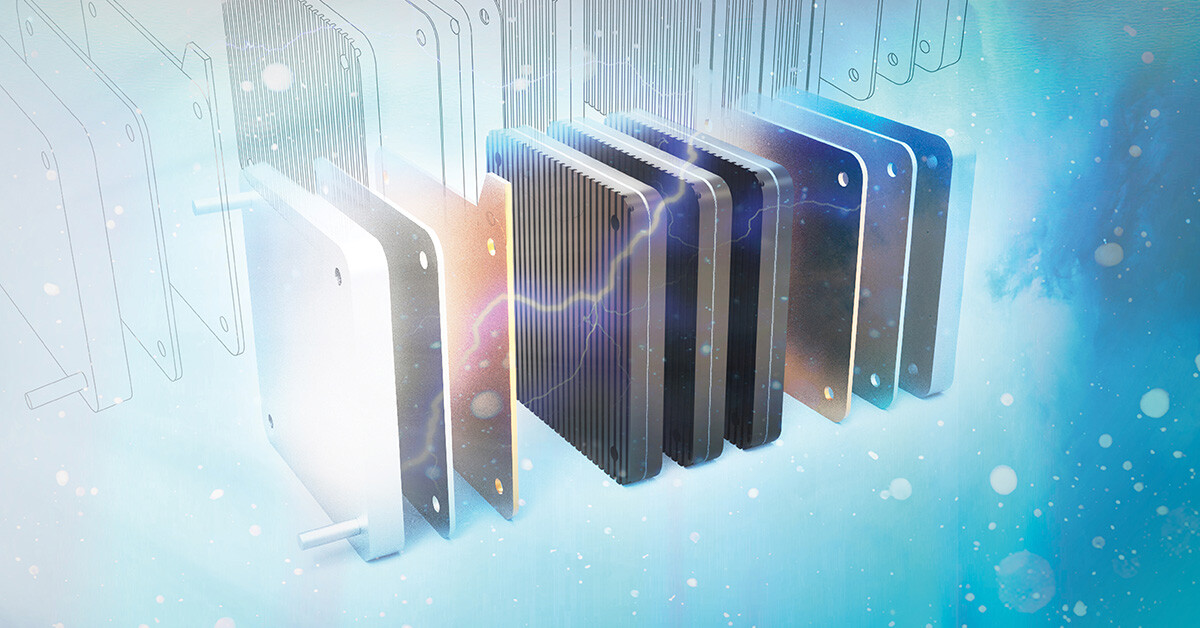
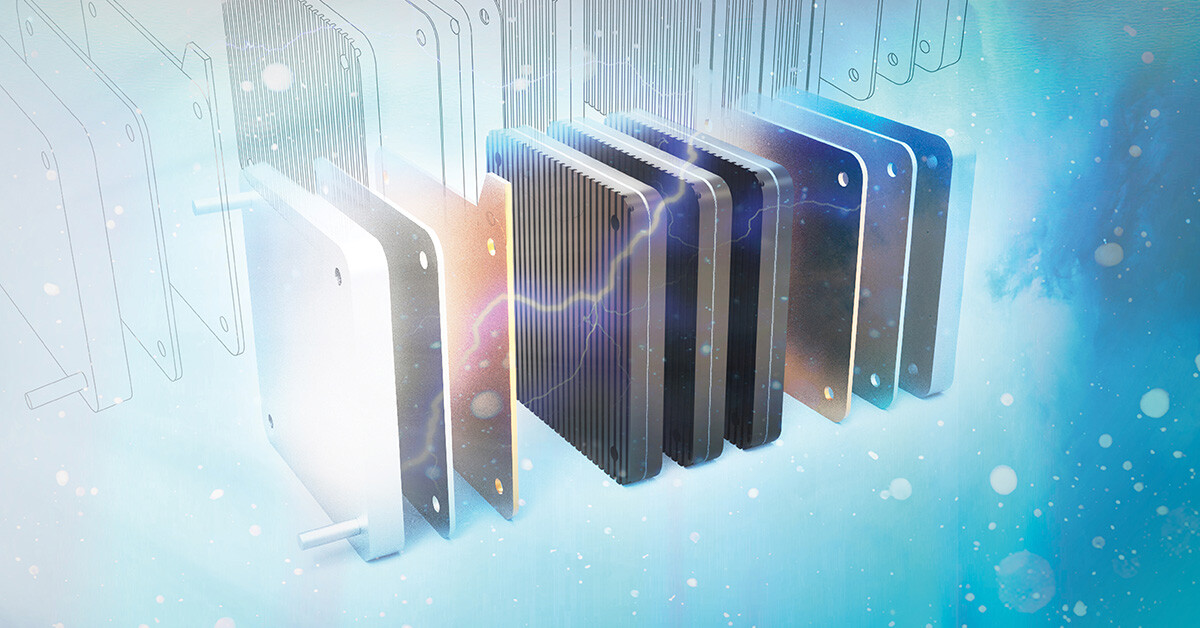
Enhancing Fuel Cell Durability and Longevity in PEMFCs
Proton Exchange Membrane Fuel Cells (PEMFC) are the most commonly used fuel cells for hydrogen energy today. Its ability to operate dynamically under changing environmental conditions makes it popular in both mobile and stationary energy supply.
Typically, these cells produce between 50 kW and 150 kW of electrical power, although systems exceeding 200 kW have recently been introduced. For applications requiring higher power, multiple stacks can be used in parallel.
The main components of a PEMFC stack are the catalyst-coated membrane (CCM) within the Membrane Electrode Assembly (MEA), the gas diffusion layer (GDL), and the bipolar plates (BPP).
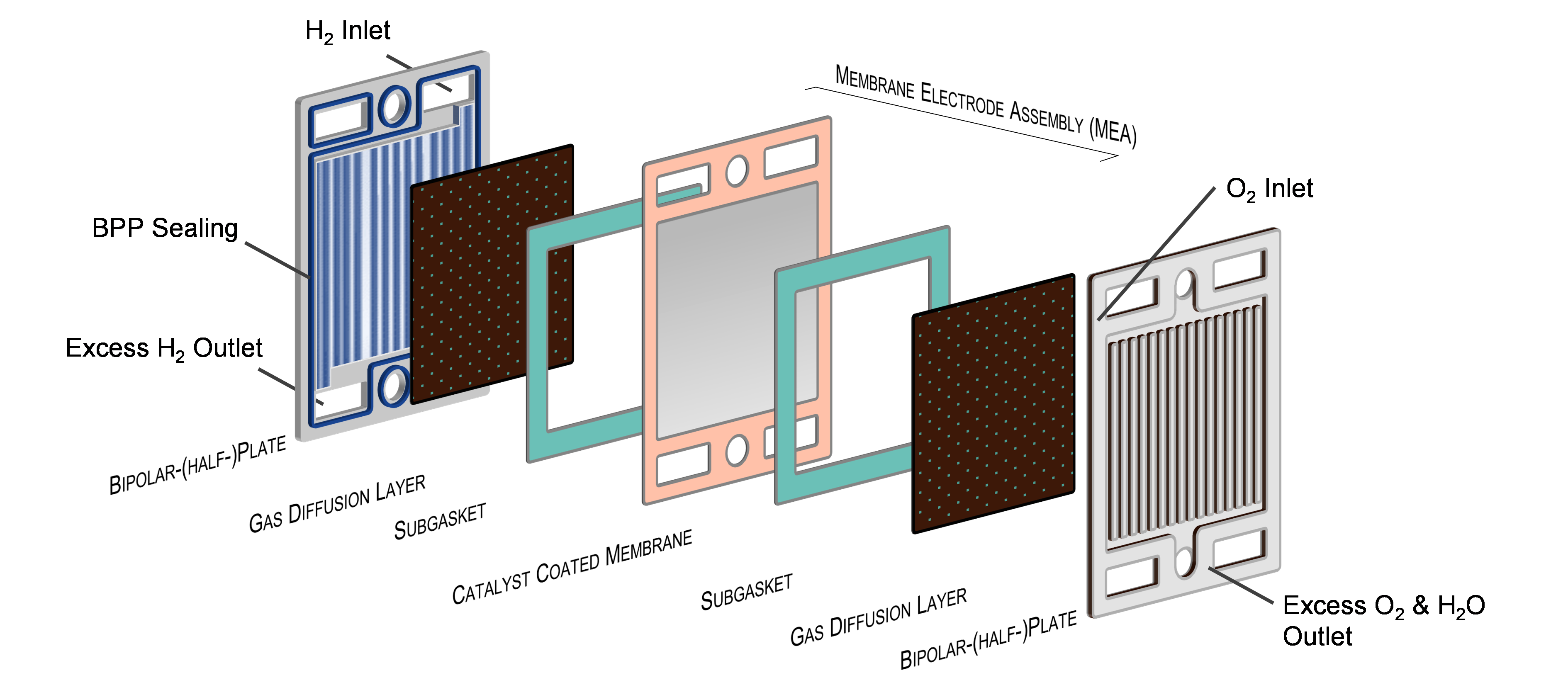
in accordance with Heimes et al. “Production of Fuel Cell Components”; PEM RWTH Aachen
The catalyst coated membranes are central components of the PEMFC, serving two main functions. Firstly, it acts as a barrier to prevent the uncontrolled mixing of hydrogen and oxygen. Secondly, it allows selective permeability to protons, ensuring that free protons and electrons separate on the anode side and migrate in one direction. This setup forces the electrons to travel through the external electric circuit before entering the cathode compartment.
Bipolar plates play a key role by dividing the individual cells in a stack. They also help evenly distribute fuel and oxygen to the electrodes through flow channels, conduct the electricity generated by the cell, and manage the removal of H20 and heat generated during operation.
The performance of PEMFC bipolar plates and membranes depend on stack design and sealing solution selection and material choices for these components greatly influence both cost and performance. According to component manufacturer Schaeffler, these bipolar plates account for 80% of the stack’s weight, so there is a natural scrutiny in getting this decision right.
Learn more about Proton Exchange Membrane Fuel Cells in our White Paper: Driving Decarbonisation: PEMFC, AFC, PEMEL & AEL Tech for Sustainable H2 Electrolysis
Membrane Thickness: All About Balance
Membrane thickness is another key ingredient in terms of both efficiency and longevity. Thinner membranes reduce resistance to ion passage, boosting efficiency, but are more likely to degrade. Thicker membranes offer better resilience but can reduce efficiency. The idea is to create a balance, with improved lifespan and performance the objective.
Versiv materials can work as a very precise, smooth and thickness-controlled decal substrate in the production of catalytic layers via decal transfer method. In a second step this substrate becomes a release liner with excellent release properties ensuring that the substrate can be removed without damaging the very costly catalytic layer.
Bipolar Plate Design: Understanding its Importance
Bipolar plates direct air or hydrogen to the membrane , enabling the electrochemical reactions that drive energy conversion or H2 production. Optimisation involves creating finer, thinner channels to maximise the active area of the membrane. This change helps gases diffuse more evenly, positively impacting the efficiency of the fuel cell or electrolyser. The gas diffusion layer (GDL) plays a role too, ensuring uniform gas spread even with fewer entry points.
Dealing with Changing Conditions in Subgaskets Design
PEM Fuel cell membranes are protected by subgaskets that act as a secondary sealing layers within MEAs. Resilient sealing solutions are essential in the design of such layers, especially under dynamic conditions. Fuel cell vehicles, for example, must cope with extreme temperature variability, posing challenges for gasket materials:
- Thermal Hysteresis: Temperature cycles can go from sub-zero to operational heat of 200°C
- Chemical Compatibility: Gaskets must cope with corrosives like coolants and activation agents.
- Material Limitations: Conventional rubber gaskets have trouble handing chemicals, while PTFE on its own doesn’s spring back enough to maintain a good seal.
Versiv Composites is collaborating in the ongoing development of sealing solutions that combine the chemical resistance of PTFE with the sealing qualities of elastomers. The purpose of such partnerships is to come up with a sealing solution of real value to fuel cell and electrolyser technologies.
PTFE Composites for Enhanced Durability
Ongoing innovation in gas barrier materials offer improvements in fuel cell stack performance and longevity. Solutions include:
- PTFE coated polyimide
- Cast PTFE film
- PTFE coated glass cotton fabrics
These materials can replace traditional rubber gaskets, which can wear out over time. Furthermore, PTFE durability offers the possibility of extending the lifespan of fuel cell components, potentially matching the lifespan of other stack parts, a potential beyond conventional rubber seals.
Conclusion
Overcoming material challenges, optimising sealing performance, and understanding operational parameters are key to enhancing the efficiency, durability, and cost-effectiveness of PEMFC and PEMEL systems. Innovations in stack design and sealing solutions are vital for continuing to influence hydrogen fuel cell and electrolyser technology.