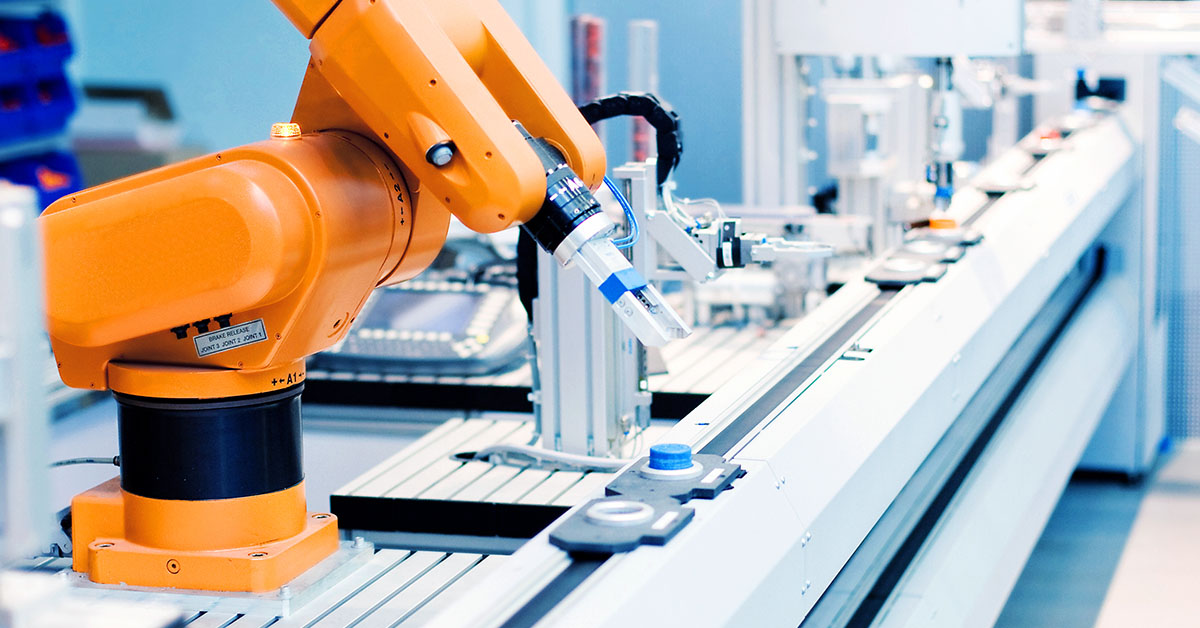
Pharmaceutical rubber stoppers are sealing components used to safely close vials and bottles, protecting drugs from contamination.
A type of rubber stopper, septa closures are highly relevant for medical laboratory automation, in which robotic technology is used to speed up and standardise laboratory tasks.
While it boosts efficiency and accuracy, automation demands closures that are highly consistent, durable, and contamination resistant. Any variation in elastomeric stoppers can compromise sterility.
Ensuring pharmaceutical safety
By combining polymer-based materials, such as Versiv PTFE Cast films, with elastomers, it is possible to manufacture reliable inert sealings that protect drug formulations from interaction with the closure itself, as well as degradation and leakages.
Versiv PTFE barrier solutions provide:
- Advanced Surface Treatment: Versiv applies high-quality etching and surface treatments to one or both sides of the film, ensuring robust bonding between the protective PTFE layer and the elastomer support. This bond is vital for preventing delamination and maintaining seal integrity.
- Customisable Barrier Layers: Versiv can add FEP or PTFE layers to boost chemical resistance and mechanical durability, allowing clients to tailor closures to their exact needs.
- Conformability: These PTFE cast films adapt to complex pharmaceutical closure designs, reducing manufacturing defects.
- Ability to withstand temperature: The excellent thermal stability and operating temperature range make the material suitable for drug containers that must undergo lyophilisation (freeze drying) and heat sterilisation because stoppers do not stick.
Properties suited to automation:
Modern laboratories rely on automation to achieve speed, accuracy, and reproducibility. Versiv composite materials are specifically designed to meet these demands:
- Low Friction, High Purity: A PTFE surface minimises friction, allowing robotic sampling needles to penetrate smoothly and consistently. This reduces wear on both closures and equipment, helping to lower maintenance needs and minimise downtime.
- Reliable Performance: A secure bond between layers ensures consistent performance in automated liquid handling systems, where even small variations can affect results.
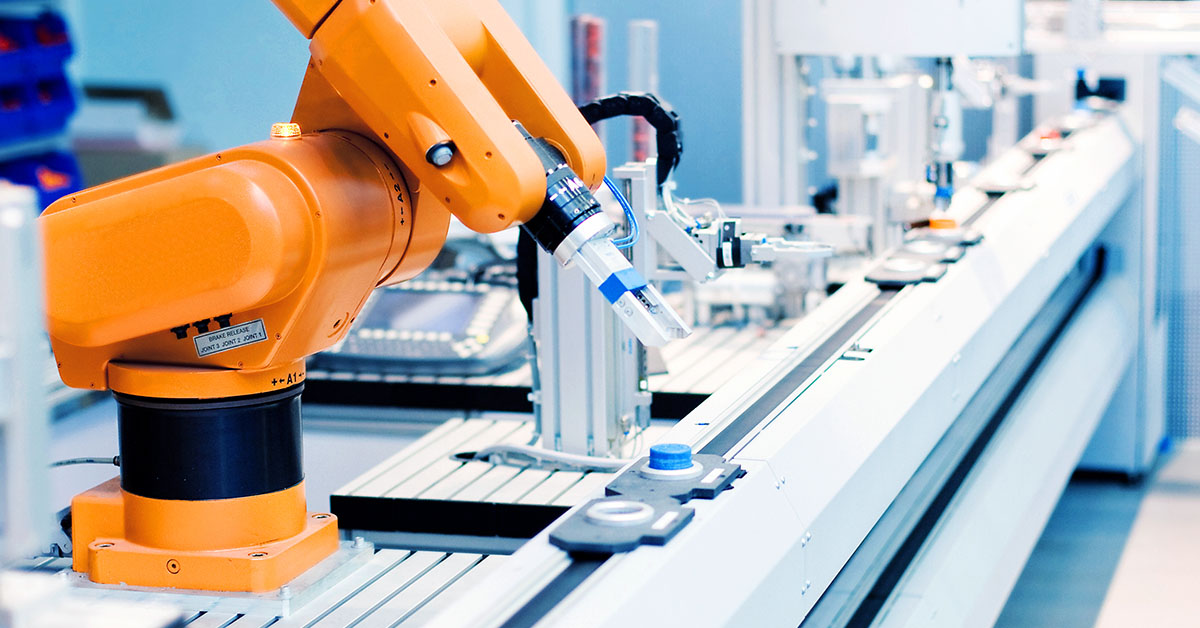
Versiv products of choice
PTFE Cast Films such as DF1700, DF1100 and DF3100 are valued materials in the pharma space.
The multilayer construction of these films has isotropic properties and uniform tensile strength, reducing the risk of pinholes or contamination. They are uniquely bondable to several sealing substrates such as butyl rubber and other elastomers.
Versiv PTFE Cast Films used in medical applications are rigorously tested by customers to meet stringent standards — keeping impurity levels below 1 ppm and safeguarding patient safety.
Chemlink® added to one surface to allow adhesive bonding.
Thickness available: 2, 4, 5 mil / 50, 100, 125 mµ
Colours available: Red, Blue, White
FEP added to one surface to allow heat bonding.
Thickness available: 1, 1.5 and 2 mil
Colours: Natural, White
Modified DF1100. Bondable on both sides.
Thickness: 4mil
Please contact our sales team for further info.
Conclusion
Pharmaceutical rubber stoppers contribute to medical drug packaging by preventing cross-contamination and maintaining product integrity. Through innovative materials and design, these closures support safer, more efficient lab and pharma operations, safeguarding both patient safety and product quality.
The use of PTFE-based materials means closures withstand repeated use, sterilisation and freeze-drying cycles without sticking or degrading. The properties of the materials deliver conformability and surface bonding that reduce the possibility of closure failures, reducing recalls and product waste. There is an additional benefit as low-friction, high-purity materials reduce wear on automated equipment, translating to fewer breakdowns and lower total cost of ownership.