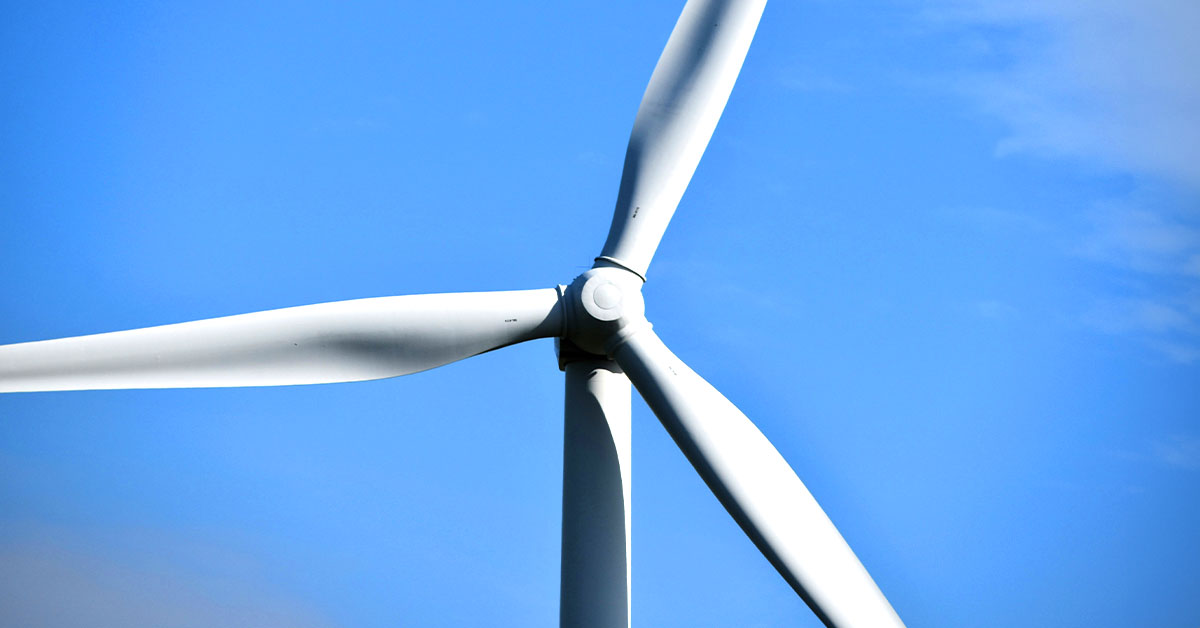
When it comes to the wind blade manufacturing process, one critical component is the choice of mold release material. Composite materials, specifically polytetrafluoroethylene (PTFE) coated fibreglass fabrics, can be transformational in terms of efficiency and bottom line.
With the growing demand for larger and more efficient turbine blades, PTFE-Coated Fabric Adhesive Tapes offer strong competitive advantages for their manufacture via molding processes. The consistent release properties of PTFE provide reduced maintenance requirements and an overall improved production efficiency. This is a combination of benefits of high value to wind turbine (or mill) producers who wish to maximise their manufacturing operations.
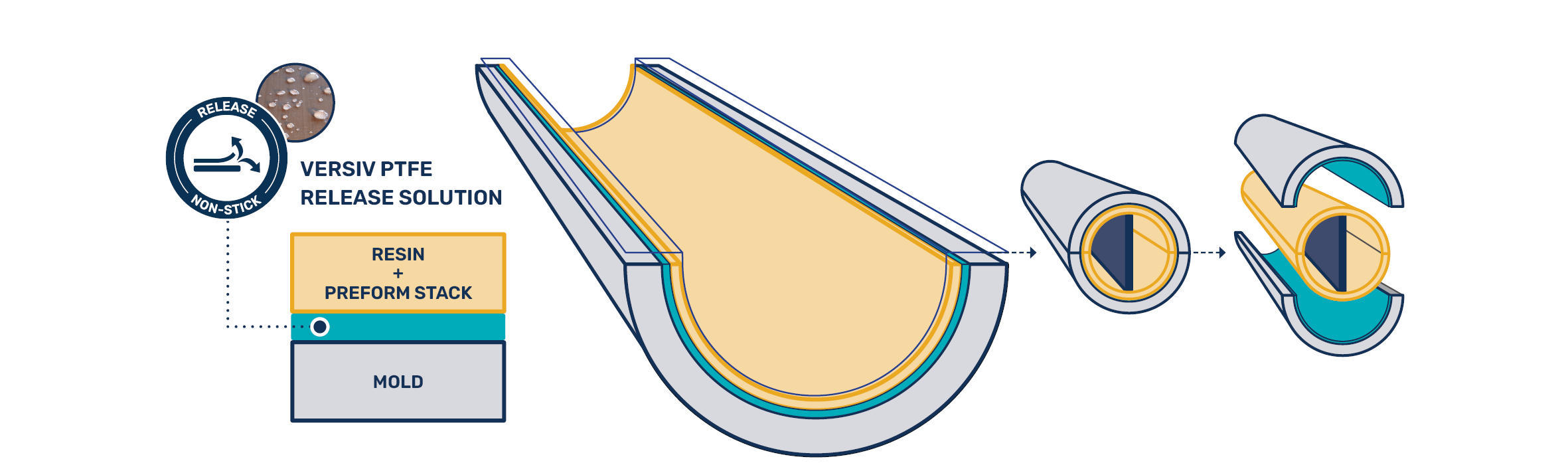
Consistent Mold Release Performance
Mold release materials must satisfy two important requirements: consistent release performance of the tape itself, and its performance in getting out of the mold once it is no longer suitable for the release function. The material must be able to perform without leaving any traces or residuals.
The silicon-based pressure-sensitive adhesive in the material sticks to the mold and provides a fine balance between bonding performance and ease of release when removing the mold covering. It must offer sufficient bonding strength during manufacturing while allowing clean separation when the mold release tape is removed.
In comparison, a standard tape that goes through several seasons deteriorates due to the application of multiple pressure and temperature cycles. The material may become more and more brittle when you peel it off due to load, pressure and temperature.
PTFE Coated Fabric Solution – CLPSA-4
Versiv CLPSA 4 PTFE-Coated Fabric Adhesive Tape is developed to meet this criterion. This laminated material, with superior release and extended durability, can undergo up to 40 pulls or reuse cycles while maintaining dimensional stability, which is significant in terms of price performance ratio.
By comparison the standard version Versiv CS305 coated fabric goes up to 10 pulls depending on the substrate and adhesive used. Using CLPSA and its ability to do 40 cycles has a knock-on effect on cost efficiency.
“The magic number is 40 - 40 pulls or cycles. This is significant in terms of price performance ratio. The standard version - CS305 Coated fabric can go somewhere under 10 pulls depending on the substrate and adhesive you use.”
PTFE Composites vs. Traditional Spray-On Releases
When compared to conventional spray-on mold releases, PTFE composite materials offer several distinct advantages.
Spray applications, while initially more economical to apply, present challenges in consistent coverage and typically require more extensive cleanup. Spray is harder to clean and must be scraped off, which can potentially damage expensive mold surfaces over time. While sprays are water-based the rework or afterwork after spray application also adds time and effort compared to using PTFE composites.
Versiv materials protect the mold physically as well. These fabrics offer physical protection to the mold surface, acting as a cushioning barrier against accidental drops or impacts during the manufacturing process-a function that sprays do not offer.
While premium materials may represent a higher initial investment, their durability translates to fewer replacements, reduced downtime, and more consistent production quality-all factors that significantly impact the total manufacturing cost over time.
Partnering for Ongoing Gains in Wind Blade Manufacture
By working closely with wind energy manufacturers to understand their specific requirements, Versiv Composites continue to refine their offerings. Whether customers require smooth finishes or textured surfaces for aerodynamic performance, adaptable PTFE release systems can accommodate these preferences while minimising defects and improving overall quality.
By providing extended reuse cycles, consistent release properties, and mold protection, these materials deliver measurable improvements in manufacturing economics while supporting the production of high-performance wind blades.
Specialised materials are an essential consideration for manufacturing decision-makers seeking competitive advantages in this rapidly growing industry.
To explore how Versiv Composites advanced coated fabrics can optimise your manufacturing process, visit our product pages or contact our team for tailored solutions.
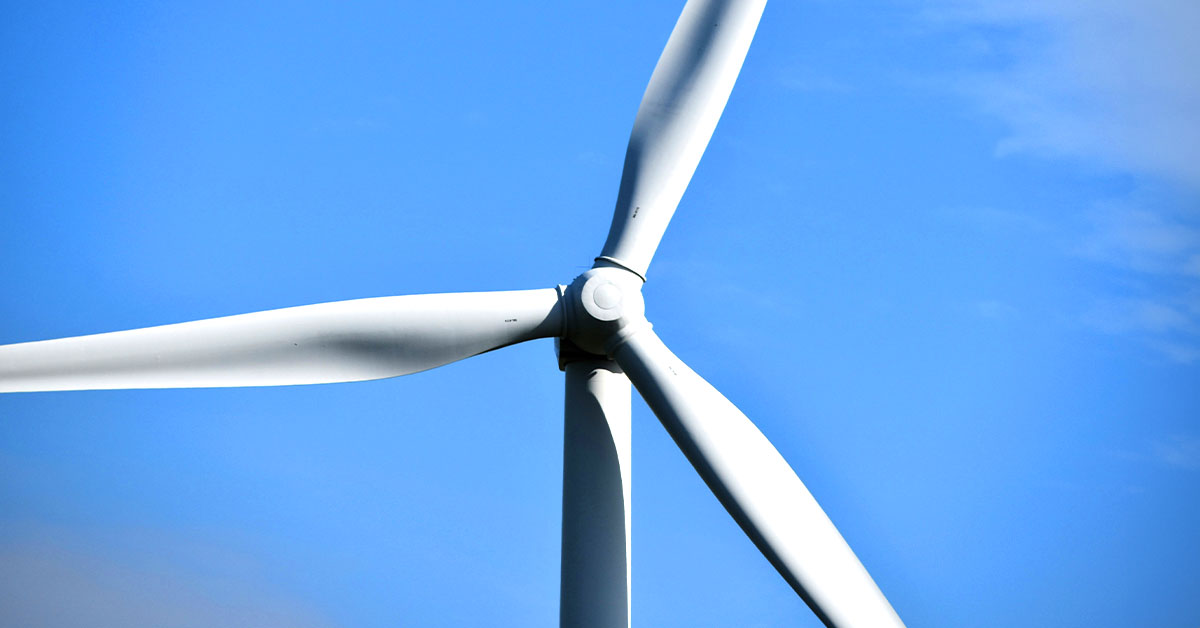