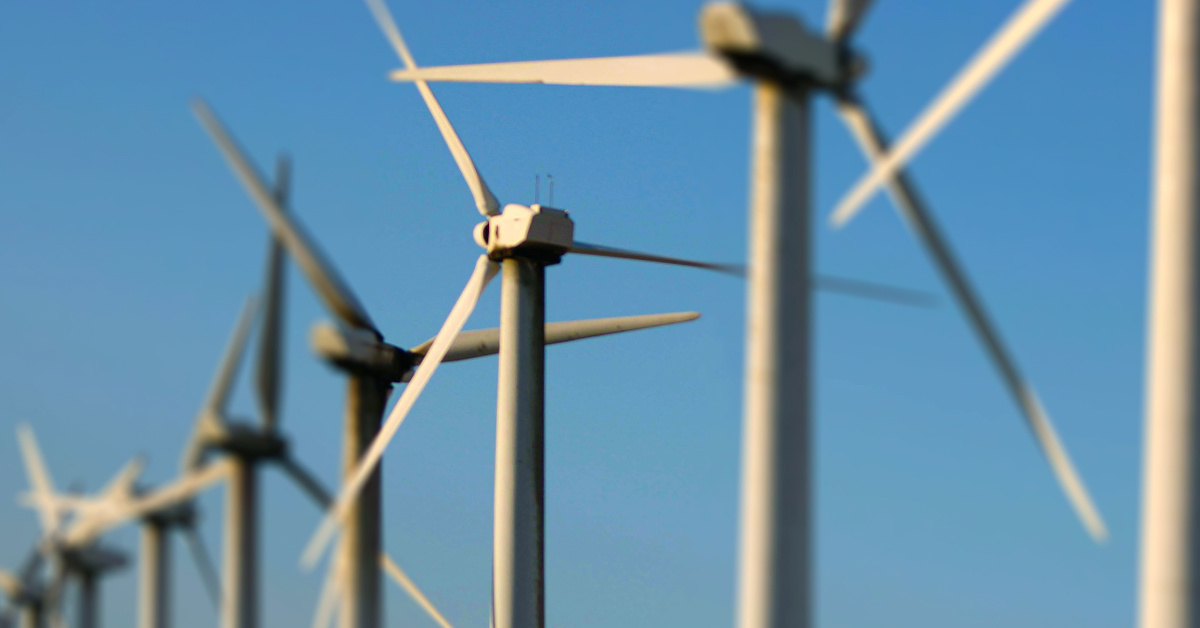
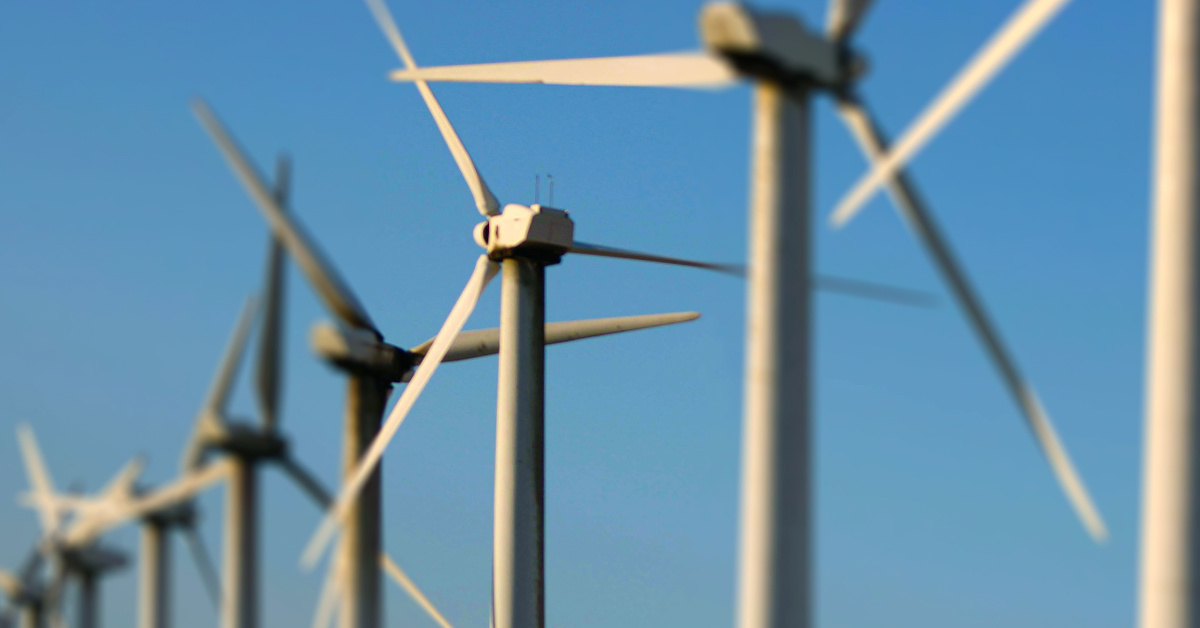
The role of PTFE composite materials in enhancing wind blade manufacture
Addressing Early Challenges in Wind Energy
I have had the privilege of witnessing the evolution of Versiv PTFE composite release materials in the wind blade manufacturing sector since we first introduced them around 2007. The renewable energy landscape has changed dramatically, and our commitment to innovation has played a role in this transformation.
Versiv PTFE mold release materials play a part in wind blade manufacturing by preventing the composite materials used in the blades from sticking to the molds during the curing process. As well as smooth release, our materials also lead to reduced defects, and because of less mold cleaning and maintenance, more efficiency. With one of our larger customers, we achieved an average of 45 pulls (release of blade from mould), without maintenance.
Enhancing Operational Efficiency
In essence, the key challenge for Versiv is to get more blades out from the mold without having to change the release materials on the mold (maintenance time) or without having to do significant rework of the blades surface (qualify of finish and time).
Adapting to Industry Demands
As wind blades have grown larger, so too has the demand for longer lengths and configurations of our PTFE mold release materials. For instance, the wind blade market increasingly relies on products like PTFE Coated Fiberglass Tapes, such as CLPSA4 S and CS305 S. These materials are selected for their multiple uses, excellent tear resistance, and the fact that they do not elongate when pulling, making them ideal for high-stress applications in wind blade manufacturing.
Additionally, we have improved the durability and heat resistance of our PTFE release films through material composition changes, including the overall improvement of adhesion. This innovation again reduces downtime and maintenance, allowing manufacturers to focus on production.
Wind blade manufacturers prefer seamless options to avoid seams that can compromise the structural integrity of the blades. By working closely with our customers, we ensure that we address diverse requirements and continuously improve our offerings.
Optimising Composite Molding Processes
Our non-stick coatings can also play a role in the manufacturing process of windmill blades. The technique involves the infusion of resin through reinforced materials covered by a nylon bag. While this method presents challenges, such as difficulties in saturating carbon fibers and achieving low fiber concentration, our PTFE materials enhance the process by improving resin flow and minimising defects during molding.
Our PTFE mold release materials contribute to reducing defects and improving surface finishes during the composite molding process. Whether customers prefer a smooth finish or a textured surface for aerodynamic performance, we adapt our products to suit their preferences.
Supporting the Growing Wind Energy Market
The global wind energy market is experiencing significant growth, particularly in the Asia-Pacific region, with onshore wind energy leading the way. As the market expands, our PTFE composite materials continue to evolve to meet the increased demand for larger, more efficient wind blades. Our commitment to innovation and customer collaboration ensures that Versiv Composites remains at the forefront.
If you’re looking to optimise your wind blade manufacturing with our advanced PTFE mold release materials, we invite you to contact us today.